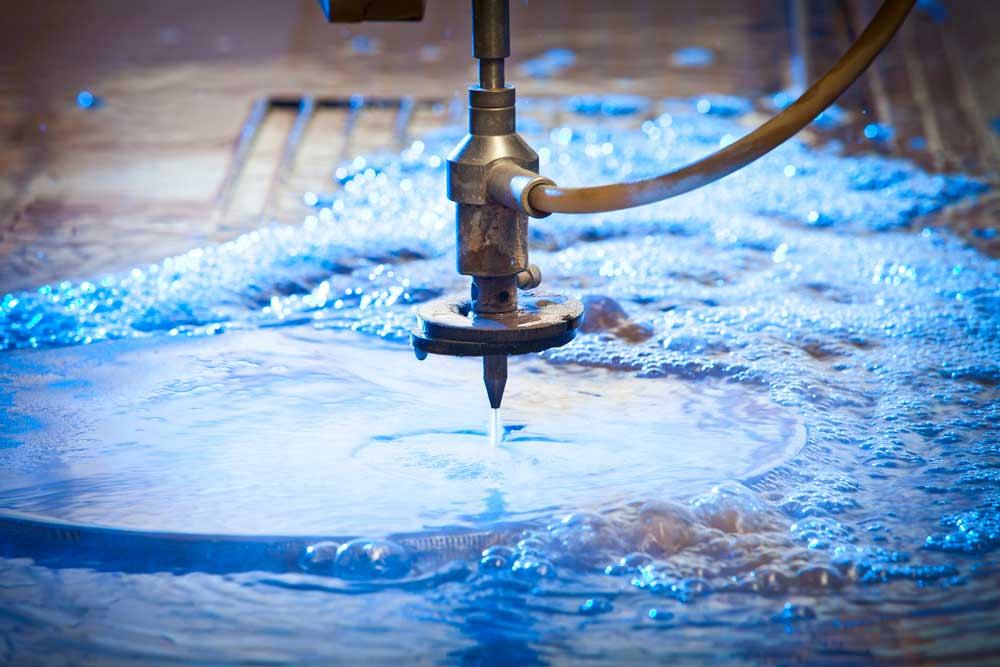
Waterjet Cutting was first commercialized in the 1970’s however struggled to gain traction in the industry due to being inaccurate. Moving forward to the 21st century, Waterjet suppliers dialed in their machines and they are now one of the most popular choices amongst shops.
Why RTD Invested in a Waterjet
Reich Tool decided to invest in a waterjet for two main reasons: versatility and simplicity. The waterjet’s versatility is demonstrated by the amount of materials and thicknesses it is able to cut. Waterjet cutting is also a very simple process due to the minimal amount of secondary work needed.
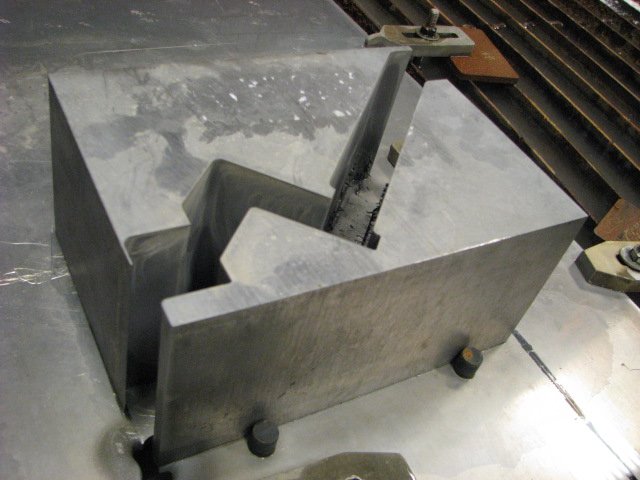
Waterjet Cutting vs. Laser Cutting
When deciding between a waterjet and a laser cutter we chose to purchase a waterjet for a few reasons. Laser cutting lacks both the versatility and cutting strength for the types of projects we handle. We waterjet projects up to 9” thick which far exceeds a laser cutters maximum capabilities which max out at a 1 ¼”. A Waterjet also allows us to cut any type of material. Laser Cutting on the other hand struggles to cut through reflective materials such as aluminum or many yellow metals like bronze or copper.
Waterjet Cutting vs. Plasma Cutting
Waterjet cutting shines over plasma cutting in three areas: quality, types of material it can cut and secondary operations. When comparing plasma cutting to waterjet cutting, plasma cutting is a much quicker process, however the surface finish of plasma cut parts are far less clean than that of a waterjet cut part. Secondly plasma cutting uses a lot of heat when cutting material. This leads to hardened surfaces and more brittle material. As a result, secondary operations are more difficult to complete i.e. tapping and beveling. Lastly a waterjet has the ability to cut materials that don’t easily melt. On the flip side, plasma cutting destroys certain materials such as laminates in the cutting process.
Waterjet Cutting vs. Flame Cutting
Lastly waterjet cutting is a superior option over flame cutting for a few reasons. Flame cutting is restrictive with the types of materials it can penetrate and is limited to just iron and steel. Waterjet cutting is notably more precise than flame cutting and creates an almost sandblasted finish in comparison to the rough edges you may find with flame cutting. Finally a waterjet only heats the material up a few degrees during the cutting process. Flame cutting creates a heat affected zone (HAZ) making post cutting operations more time consuming and costly.

Reich Tool’s Waterjet Capabilities
Our waterjet has a table size of 6’ x 12’ and is capable of cutting parts up to 9” thick. We have helped out numerous customers with cutting common and uncommon materials ranging from steel, aluminum, phenolic, wood, laminates, and even glass to name just a few. We are able to hold +/- .005 on most parts with a typical kerf of around .040. Interested in learning more about our waterjet capabilities? Click here!
Reich Tool Overview
For over 55 years Reich Tool & Design has been building complex metal stamping dies for a multitude of industries. In addition to building dies and fixtures, RTD provides high quality CNC machined and turned components. Trinity Precision Solutions (a sister company located within Reich Tool & Design) has a class 10,000 cleanroom, where they provide cleanroom assembly, cleanroom packaging, and ultrasonic washing with citric passivation. Feel free to send in your RFQ by clicking here.