With increased demand for tighter tolerances & better surface finishes at a lower cost per part, Wire EDM (Electrical Discharge Machining) is a very qualified manufacturing alternative. With thirty years of experience, our competency and skill with Wire EDM allow us to produce highly complicated contoured shapes with repeatable tolerances as tight as ±.0002”, easily machine critical features, sharp corners, deep cavities, and tapers (External or Internal) up to 30°.
The parts typically are manufactured completely free of stress or distortion, due to the Wire EDM process, which involves feeding a thin metal electrode through a metal work piece submerged in a tank of de-ionized water. An electric spark, that is carefully controlled, is generated between the electrode and the work piece. It produces an intense heat that liquefies the surrounding material & creates a smooth, clean, and absolute cut. The fluid also acts as a coolant and flushes away the excess material.

- 31” X 23” X 20” Travel
- 53″ X 43″ X 20″ Max Work Piece
- Fully Submersible
- Auto Wire Thread
- 4-Axis Capability
- EDM Hole Drilling
We have increased our capacity to produce parts up to 53” X 43” X 20” in size with our multiple submersible Mitsubishi CNC Wire EDM machines equipped with fully automatic wire threading and 4-Axis capabilities. To enhance our capabilities, we can also EDM drill narrow holes from .015″ to .150” in diameter.
Along with a collection of ferrous and non-ferrous materials, we also process hard metals and exotic alloys, used in aerospace and medical fields, at a level of precision not possible using other machining methods.
We produce parts that are accurate, burr-free, and have fine exceptional surface finishes as a result of our extensive manufacturing capabilities.
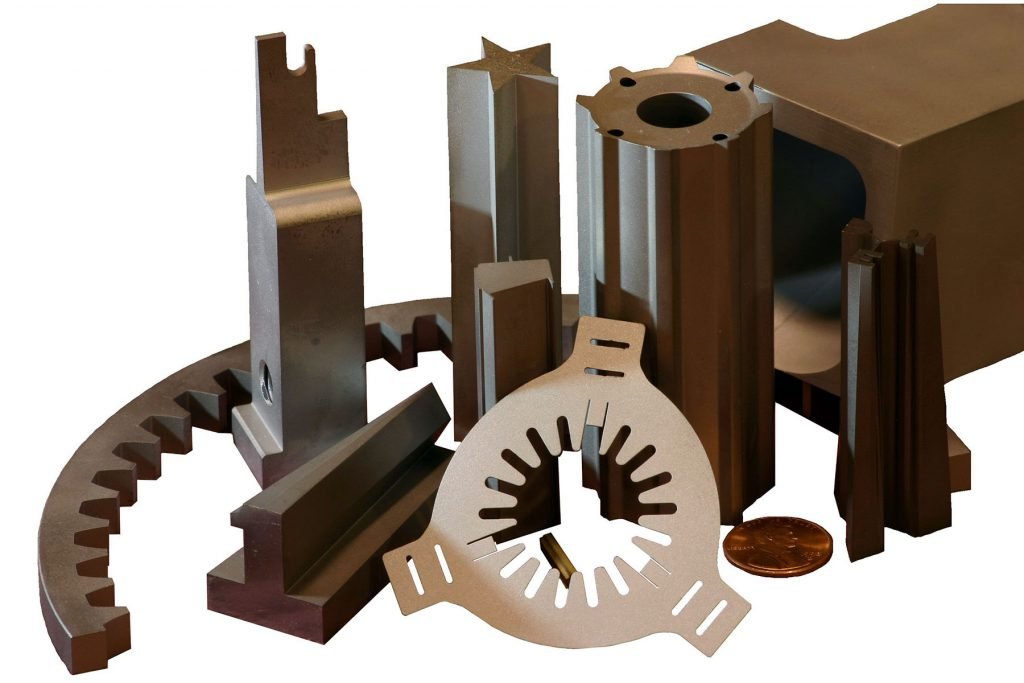